Theme: Research
PhD defence of Clément Raimbault
Clément Raimbault defends his PhD in Numerical Mechanics and Materials on Nov. 25, 2021
"Foaming of polyurethane injected on a porous material"
Clément Raimbault conducted his PhD under the supervision of Patrice Laure, Michel Vincent and Séverine Boyer. Je defends his PhD in Numerical Mechanics and Materials on Nov. 25th, 2021 in front of the following jury:
Abstract:
Polyurethane foams are sometimes combined with a porous layer to improve physical properties like sound and thermal insulation in the automotive industry. Such parts are manufactured by a reactive injection molding process, with a porous medium positioned beforehand on one of the cavity walls. A mixture composed of polyol, isocyanate and water is then injected in the closed cavity. The reaction between isocyanate and water creates carbon dioxide bubbles. Simultaneously, polymerization of polyurethane occurs resulting from the polyol and isocyanate reaction. The expanding foam fills the cavity and a part of the porous layer. The objective of this work is to develop a macroscopic model to simulate the influence of the porous medium on the mixture flow inside the cavity along with the evolution of temperature and pressure in the foam. Foam density, bubble size distribution and impregnation of the porous medium are also studied. First, foaming parameters are identified with the FOAMAT® device and experiments are performed to measure density, porosity and permeability values of a porous material. Then, foam injection tests are carried out on a stantard square mold geometry, with a porous layer on its lower wall. The cell size distribution is identified from scanning electron microscopy and micro-tomography image analyses. Numerical simulation is realized with REM3D® software. To model the foam flow in the porous medium, the Navier-Stokes-Brinkman model is coupled with the foaming model. After the implementation of this model, the upgraded REM3D® version is used to check the model by comparison with experimental data. Correlations are made between the size of bubbles, the density and temperature fields, the penetration depth of the foam in the porous medium and the permeability.
Keywords: injection, foam, polyurethane, porous, numerical simulation
PhD defence of Ramy Nemer
Ramy Nemer defends his PhD on Nov. 23rd, 21
An adaptive immersed mesh method for fluid-structure interaction
PhD defence of David Xu
David Xu defends his PhD in Numerical Mechanics and Materials on Nov. 4, 2021
Thermomechanical analysis of the Fused Filament Fabrication process: Experimental and numerical investigations
David Xu conducted his PhD work in CFL team, under the supervision of Franck Pigeonneau. David Xu defends his PhD in Numerical Mechanics and Materials on Nov. 4th, 2021 in front of the following jury:

PhD defence of Juhi Sharma
Juhi Sharma defends her PhD in Numerical Mechanics and Materials on October 22, 2021
Microstructural evolutions during hot forging of VDM Alloy 780: mechanisms, kinetics and mean field modelling
Juhi Sharma conducted her PhD work in MSR team, under the supervision of Nathalie Bozzolo et Charbel Moussa. She defends her PhD in Numerical Mechanics and Materials on Oct. 22nd, 2021 in front of the following jury:
- Pr. RAE Catherine (Univ. of Cambridge – Materials Science and Metallurgy, Royaume-Uni)
- Pr. KESTENS Leo (Ghent Univ. Technologiepark Zwijnaarde, Belgique)
- Pr. BERNACKI Marc (MINES ParisTech-CEMEF, Sophia Antipolis)
- I.R. GEHRMANN Bodo (VDM Metals international, Altena, Germany)
Abstract:
The demand to reduce the emission levels in aircraft engines has motivated the development of new high temperature alloys. VDM Alloy 780 is a new polycrystalline nickel-based superalloy, developed for turbine disc applications, with higher service temperatures up to 750°C. VDM Alloy 780 comprises of γ′ strengthening phase, in addition to the grain boundary plate-like precipitates which are identified as η/δ phase (mostly η phase but likely to include thin δ layers). A precise evaluation of the microstructural evolutions during the multistep industrial forging operations is crucial to the final properties of the alloy. Through a series of isothermal heat treatments, microstructural analyses, advanced EBSD techniques and electrical resistivity measurements, a detailed description of the precipitation behavior, associated precipitate shape and size evolutions as well as the grain growth kinetics were obtained. Hot compression tests were designed in accordance with the industrial forging conditions to determine the recrystallization mechanisms and kinetics in the supersolvus domain. The dynamic and post-dynamic recrystallization kinetics were established in function of the thermomechanical parameters such as strain, strain rate, temperature and post-deformation holding time. A mean field model was calibrated based on those experimental results and proved to be capable of correctly predicting the microstructural evolutions in the single-phase domain. In addition, the influence of the second phase particles on the recrystallization behavior in the subsolvus domain was investigated. This work provides guidelines to optimize the industrial forging conditions for this new superalloy to obtain a homogenous and fine-grained microstructure.
Keywords: Polycrystalline nickel-based superalloys, hot forging, recrystallization, grain growth, precipitation, mean field modelling
PhD defense of Gabriel Manzinali
Gabriel Manzinali defends his PhD in Numerical Mechanics and Materials on July 16th, 2021
"Adaptive control for iterative solvers in an FE framework with mesh adaptation, for CFD simulations of industrial processes"
Gabriel Manzinali conducted his PhD work in CFL team, under the supervision of Elie Hachem, Youssef Mesri and Aurélien Larcher. Gabriel Manzinali defends his PhD in Numerical Mechanics and Materials on July &-th, 2021 in front of the following jury:
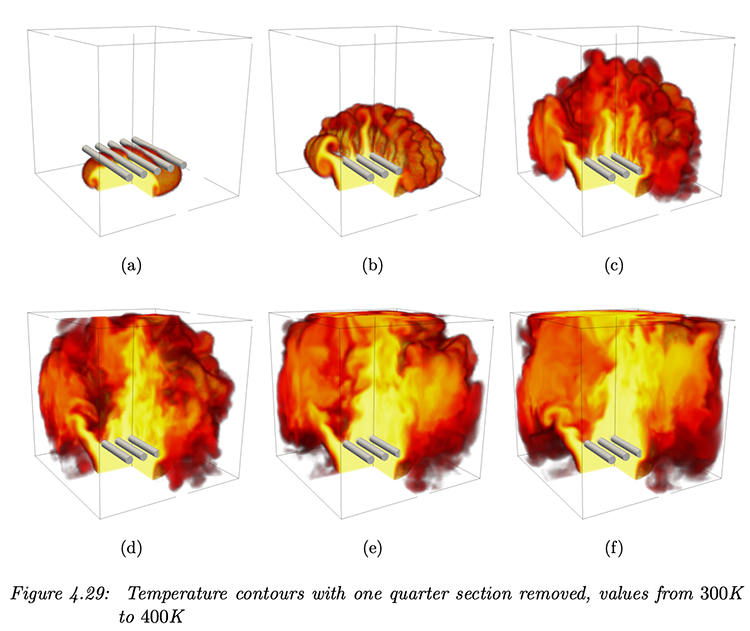
PhD defence of Jules Baton
Jules Baton defends his PhD in Numerical Mechanics and Materials on June 4th, 2021
Dislocation structures in cold deformed pure tantalum: evolutions and influences on recovery and recrystallization
Jules Baton conducted his PhD work in MSR team, under the supervision of Nathalie Bozzolo et Charbel Moussa and in the framework of research project with CEA. Jules Baton defends his PhD in Numerical Mechanics and Materials on June 4th, 2021 in front of the following jury:
Abstract:
