Theme: Research
PhD defence of Matheus Brozovic Gariglio
Matheus Brozovic Gariglio defends his PhD in Computational Mechanics and Materials on Feb. 2, 23
A multiscale study of microstructural evolutions in hot-deformed two-phase titanium alloys
Matheus Brozovic Gariglio conducted his PhD work under the supervision of Nathalie Bozzolo (MSR team) and Daniel Pino Munoz (CSM team). He defends his PhD in "Computational Mechanics and Materials" on February 2nd, 23 in front of the following jury:
Juhi Sharma, winner of the 2nd Bodycote SF2M 2022 prize
La SF2M récompense les travaux de thèse de Juhi Sharma par son prix bodycote.
The French Society of Metallurgy and Materials, SF2M, has awarded its 2nd Bodycote prize to Juhi Sharma, PhD from CEMEF.
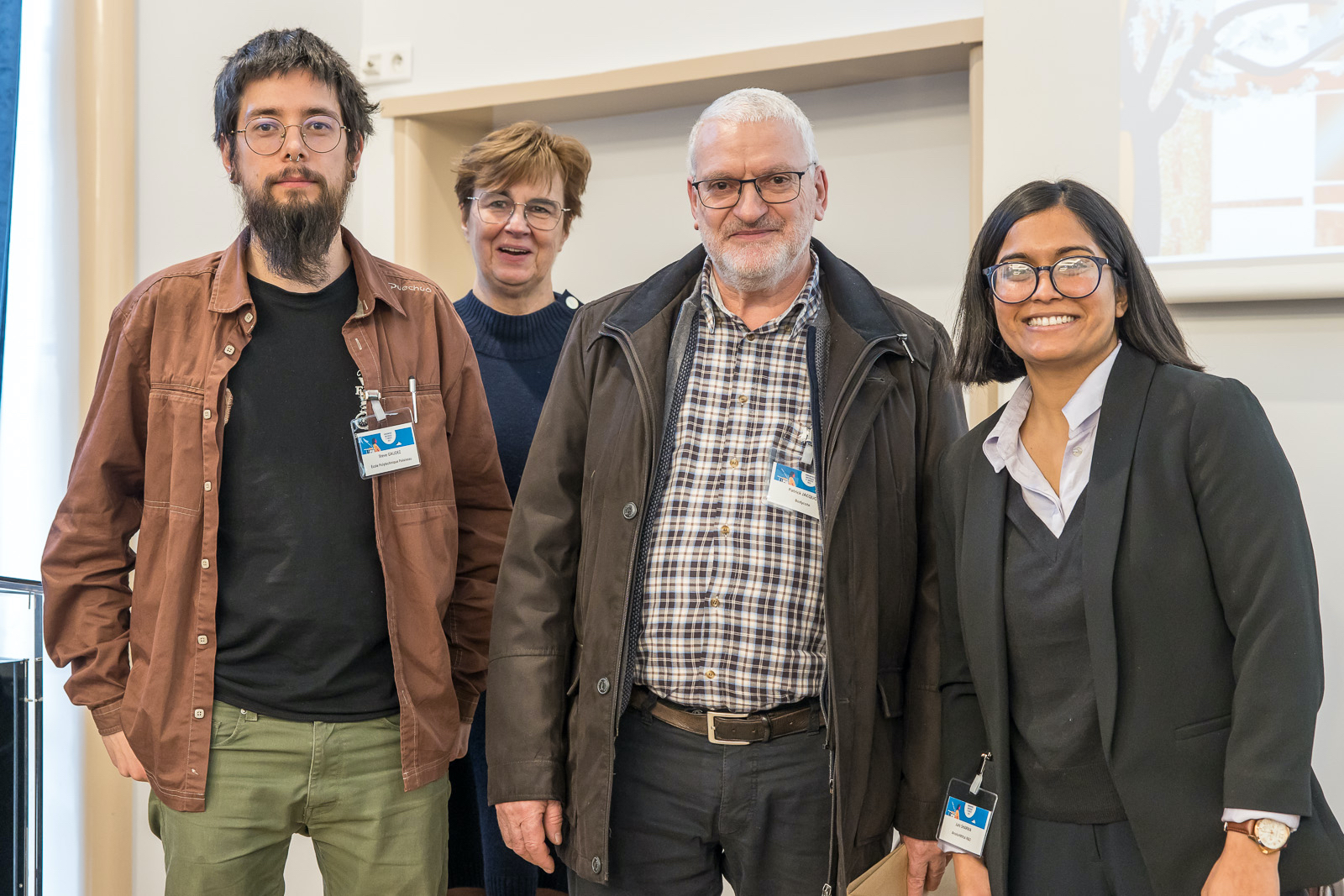
PhD defence of Emile Hazemann
Emile Hazemann defends his PhD in Computational Mechanics and Materials on Dec. 19, 22
Study of recrystallized grains occurence in single crystal nickel-based superalloys for turbine blades application
Emile Hazemann conducted his PhD work under the supervision of Charles-André Gandin, Michel Bellet, Yancheng Zhang (2MS team) and Karim Inal (PSF team). He defends his PhD in "Computational Mechanics and Materials" on December 19, 22 (subject to the agreement of the reviewers) in front of the following jury:

PhD defence of Yijian Wu
Yijian Wu defends his PhD in Computational Mechanics and Materials on Dec. 13, 22
Developments and applications of a multi-scale numerical method coupling the Cellular Automaton and Parabolic Thick Needle methods for the prediction of dendritic grain structures
Yijian Wu conducted his PhD work under the supervision of Charles-André Gandin and Oriane Senninger (2MS team). He defends his PhD in "Computational Mechanics and Materials" on December 13, 22 (subject to the agreement of the reviewers) in front of the following jury:
Abstract:
Keywords: solidification, modeling, multi-scale, Cellular Automaton, Parabolic Thick Needle, dendritic microstructure
Solidification front of the bi-crystal CAPTN simulation, presented by (a) needle network, (b) composition field in PTN finite element mesh, and (c) automaton cells
PhD defence of Sacha El Aouad
Sacha El Aouad will defend his PhD in Computational Mathematics, High Performance Computing and Data on Dec. 9, 22.
Numerical and parallel modeling of anisotropic fitted mesh for industrial quenching applications.
Sacha El Aouad conducted her PhD work in the CFL team under the supervision of Elie Hachem and Aurélien Larcher. She will defend hers PhD in Computational Mathematics, High Performance Computing and Data, on December 9, 22 in front of the following jury:
Abstract:
Keywords: Immersed methods, Anisotropic Adaptation, Numerical modelling, Fitted Mesh, Level-set function, CFD
PhD defence of Victor Grand
Victor Grand defends his PhD in Computational Mechanics and Materials on Dec. 5th, 22
"Characterization and modeling of zircaloy-4 recrystallization during hot forming"
Victor Grand conducted his PhD work under the supervision of Marc Bernacki (MSR team). He defends his PhD in "Computational Mechanics and Materials" on December 5, 22 (subject to the agreement of the reviewers) in front of the following jury:
Abstract:
