Phd defence of Mohamed Mahmoud
30 June 2022
Mohamed Mahmoud defens his PhD in Computational Mechanics and Materials on June 30, 22.
A 3-D Multi-physics computational model for thin sheet metal forming processes : Application to deep drawing and magnetic pulse forming processes
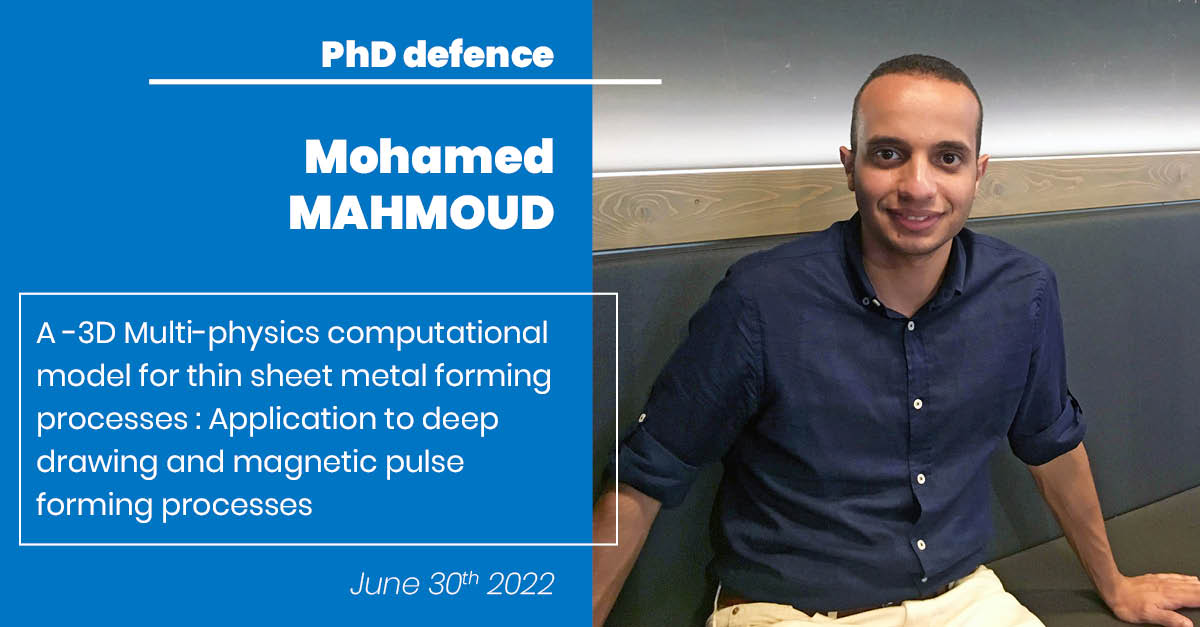
Mohamed Mahmoud conducted his PhD work in the CSM team under the supervision of François Bay and Daniel Pino Munoz. Il defends his PhD in Computational Mechanics and Materials on June 30th, 22 in front of the following jury:
– Prof. Diego Celentano, Pontificia Universidad Católica de Chile
– MC Tudor Balan, ENSAM Metz
– Prof. Guillaume Racineux, Institut de Recherche en Génie Civil et Mécanique – UMR6183, Ecole Centrale Nantes
– IR Christine Beraudo, Transvalor
Abstract:
The core of this work is focused on the development of an efficient 3D computational tool for modeling thin sheet metal forming processes using advanced remeshing and parallel computations techniques.
One of the main topics lies in the implementation of a prism division algorithm and a prismatic solid-shell element formulation in the tetrahedral-based FORGE3 software. A partitioning algorithm has been adapted in order to enable distributed memory computation.
The proposed methodologies offer a numerical tool that is capable of handling various sheet metal forming applications such as: (1). Unconstrained cylindrical bending problem for a highly bending-dominant thin structure plastic deformation; (2). Deep drawing process in which the anisotropic plastic behavior of sheet metal comes more prominent and affects the accuracy of the predicted earing profile; (3) Electromagnetic forming processing with the direct and indirect forming process which is a direct application of the multi-physics interaction between the mechanical solver and Electromagnetic solver.
Comparisons with standard mixed finite element formulations have been performed and show the superiority of solid-shell elements for most thin sheet metal forming processes with dominant high bending effects. These computations also enable a large reduction of computational time while retaining high accuracy. Moreover, a new remeshing strategy for enabling the tetrahedral remesher to generate prism-compatible meshes for the new element has been developed and will open the way for additional sheet metal forming applications.

Keywords: Solid-shell finite elements, Reduced integration, Anisotropic plasticity, Sheet Metal, Electromagnetic Forming, Deep Drawing